Horizontal Pressure Leaf Filter
Horizontal pressure leaf filter is liquid filtration system consisting of many leaf-shaped filter elements that are stacked inside a horizontal vessel.

Quality Materials

Experienced Team

Unique Technologies
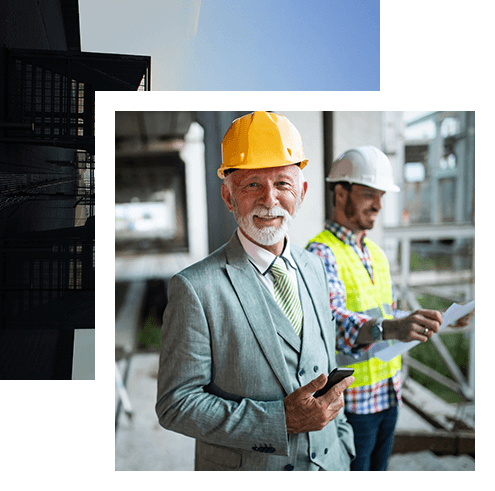
30+ Years of Experience
Our team of Mechanical, Electrical, and Process engineers do the heavy lifting and work with our customers every step of the way to develop, design, test, and refine pressure leaf filters.
Successfully Project Finished
Year of experience with Proud
Annual production capacity
High repurchase rates
Pressure Leaf Filter One-stop Service
Vertical pressure leaf filter, Horizontal pressure leaf filter, Pressure leaf filter elements
Applications
Horizontal pressure leaf filters have been widely used in many sectors,
including food & beverages, minerals & mining and chemical industries.

Food and Beverage

Petro Refining

Minning

Metal Finishing

Various

Acid and Brine
Horizontal pressure leaf filter working principle
Horizontal Pressure Leaf Filters are ideal for solid-liquid separation & work on principle of precoating & pressure.
Pre-coating is done with the help of suitable filter aid about 0.5 to 1% (Bleaching earth, diatomite, activated carbon, etc.) mixed with the liquid to be filtered. Unfiltered liquid is pumped into the filter vessel. Initially the filter aid starts forming a precoat layer on both sides of the filter leaves, until then cloudy material comes out of the filter. Once the layer is formed, pressure starts developing, restricting the impurities. Clear liquid flows from both sides into the leaves (filter elements), flows along the tubular channel & gets discharged from bottom of the leaf. All the leaves are mounted on a common manifold. The leaves start getting choked on both the sides by impurities forming cake, which is in wet from. Once the leaves get choked completely, the pressure rises to 3 kg/cm2 & the output flow almost stops. This means the batch size is reached. The pump is stopped & steam / air pressure is applied from the top (without dropping the filter pressure) to filter the material around the leaves held up in the tank & to squeeze the cake further & reduce the liquid retention in it. The holdup unfiltered liquid in the vessel portion is taken back.
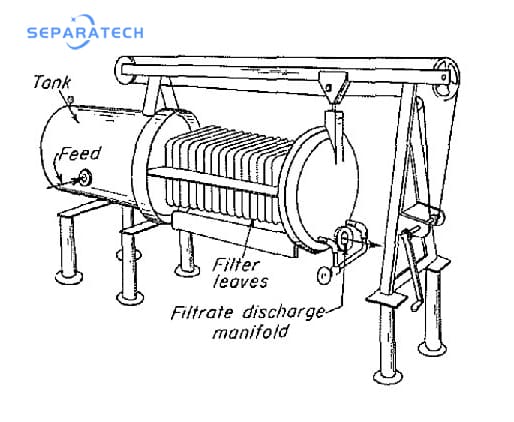
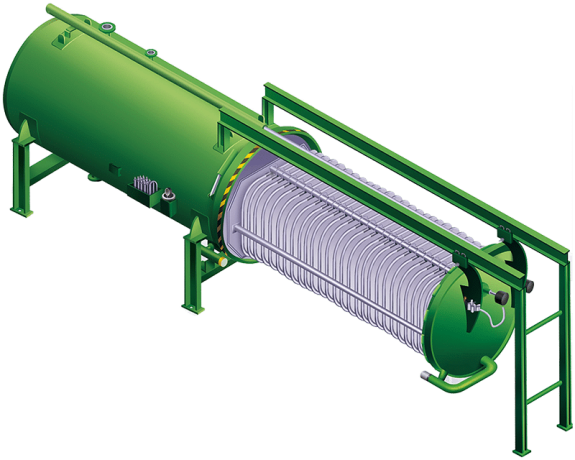
Time has changed
What are you looking for?
Normally, it takes about 8-10 weeks from order confirmation to arranging shipment. Filters of different configurations may require less or longer time.
Yes, we supple pressure leaf filter element customization service. Just provide our professional team with some necessary dimensional and specification data, and we can provide a complete set of new leaves that can replace the existing leaves.
Yes, according to different working conditions, we will provide different woven metal meshes, e.g Plain dutch weave , Reversed plain dutch weave, Dutch twilled weave, Square weave and so on.
SPECIFICATIONS
model | filter area m2 | no. of leaves | leaf spacing | height mm | height mm | vessel vol. L | floor area occupied mm |
---|---|---|---|---|---|---|---|
HPLF15 | 15 | 20 | 80 | 1800 | 900 | 1.5 | 6200X2000 |
HPLF20 | 20 | 26 | 80 | 1800 | 900 | 1.8 | 6800X2000 |
HPLF25 | 25 | 21 | 90 | 2500 | 1200 | 2.7 | 6400X2300 |
HPLF30 | 30 | 25 | 90 | 2500 | 1200 | 3.4 | 6800X2300 |
HPLF35 | 35 | 20 | 100 | 2700 | 1400 | 4.5 | 7100X2500 |
HPLF40 | 40 | 19 | 100 | 2850 | 1500 | 4.8 | 7000X2600 |
HPLF45 | 45 | 18 | 110 | 2860 | 1600 | 6.4 | 7200X2800 |
HPLF50 | 50 | 20 | 110 | 2860 | 1600 | 6.5 | 7400X2800 |
HPLF60 | 60 | 24 | 110 | 2860 | 1600 | 6.8 | 7800X2800 |
HPLF70 | 70 | 22 | 110 | 3100 | 1800 | 8.2 | 7600X3000 |
HPLF80 | 80 | 25 | 110 | 3100 | 1800 | 8.7 | 8000X3000 |
HPLF90 | 90 | 28 | 110 | 3100 | 1800 | 9.2 | 8400X3000 |
HPLF100 | 100 | 31 | 110 | 3100 | 1800 | 9.7 | 9200X3000 |
HPLF120 | 120 | 28 | 120 | 3300 | 2000 | 12.5 | 9800X3400 |
HPLF140 | 140 | 36 | 120 | 3300 | 2000 | 15.5 | 12000X3400 |
HPLF160 | 160 | 36 | 120 | 3300 | 2000 | 15.5 | 12000X3400 |
HPLF180 | 180 | 36 | 120 | 3300 | 2000 | 15.5 | 12000X3400 |
HPLF200 | 200 | 36 | 120 | 3300 | 2000 | 15.5 | 12000X3400 |
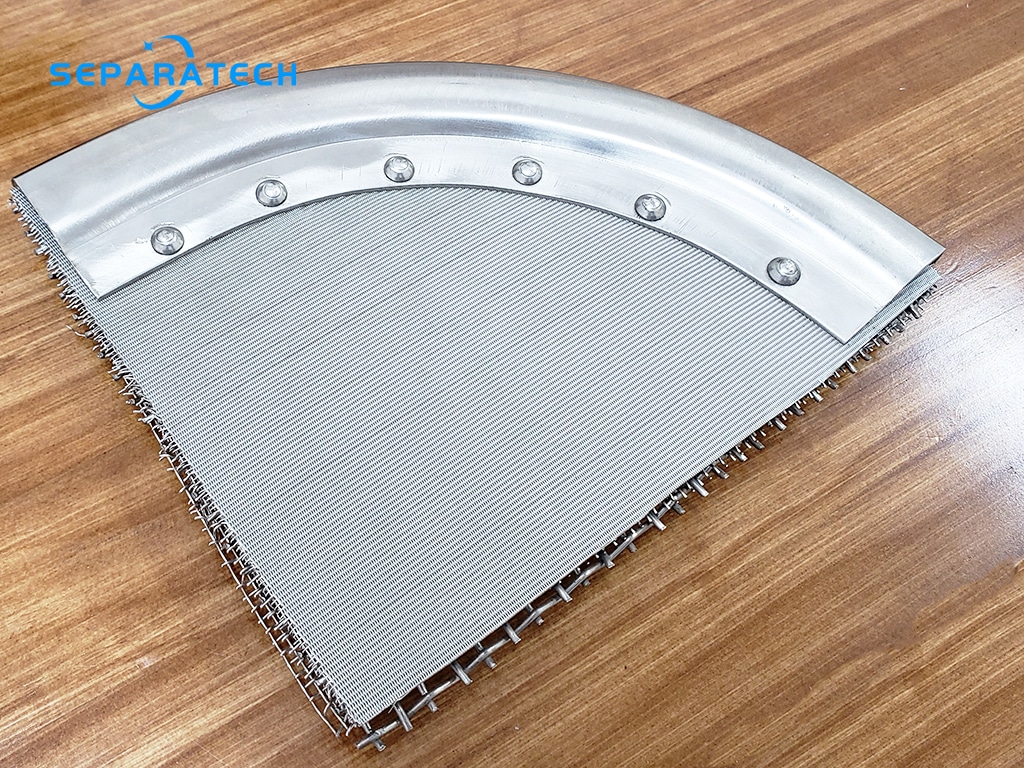
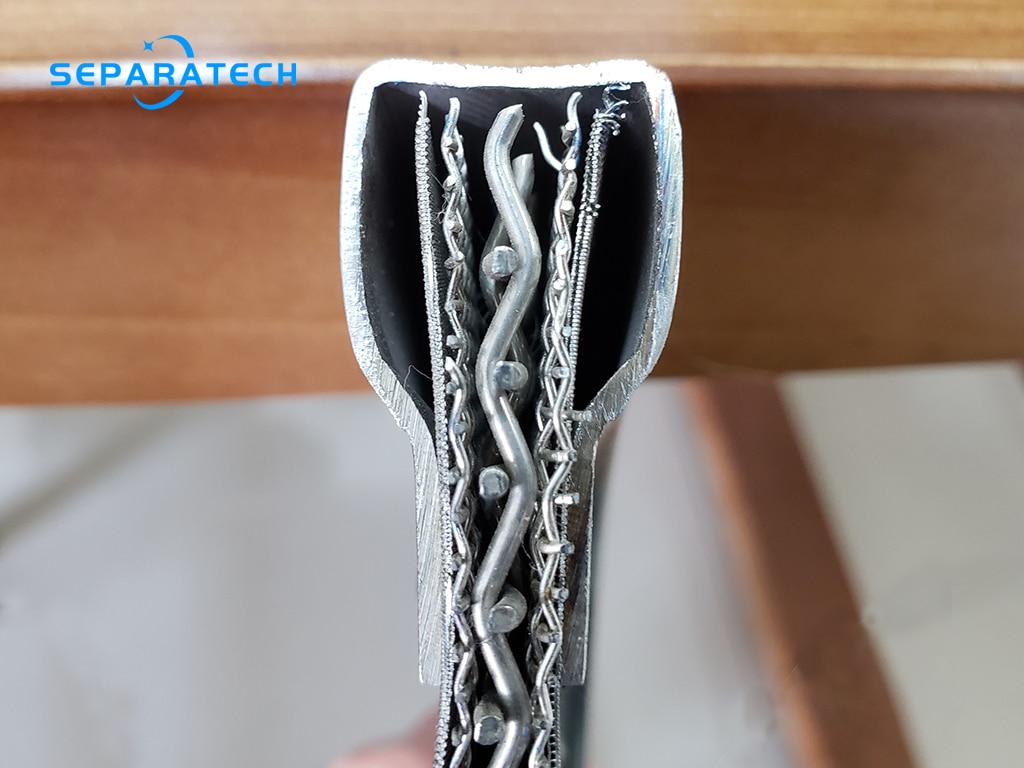
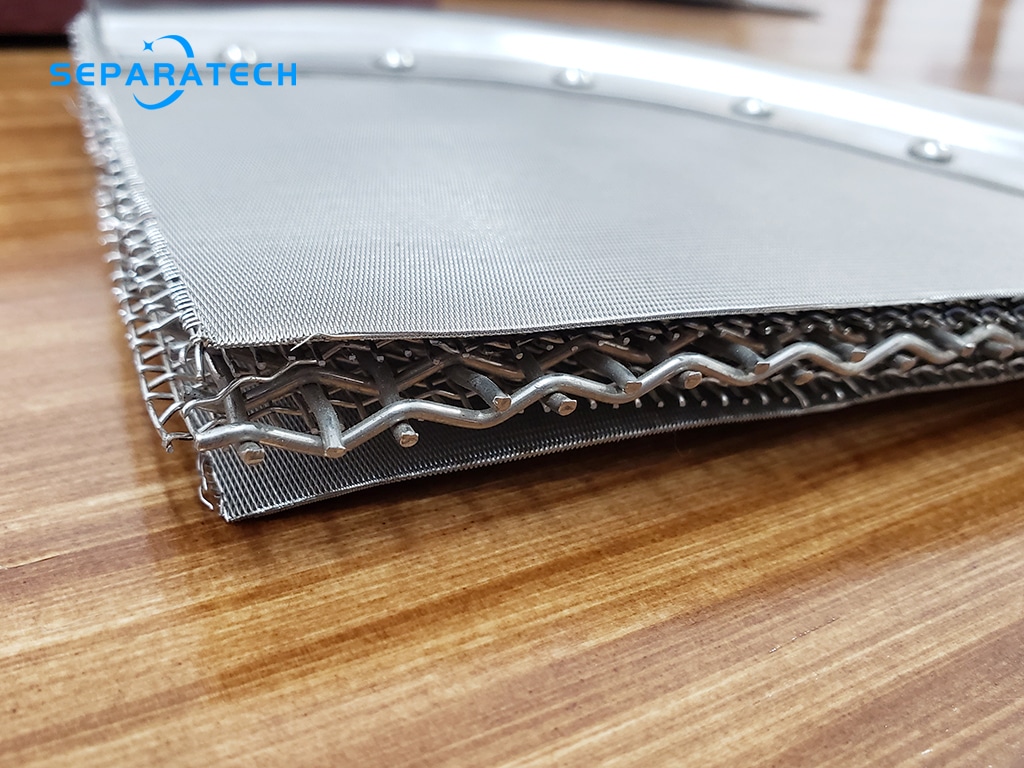