Pressure leaf filter for oil bleaching
Edible oil bleaching process
Edible Oil / cooking oil bleaching is a step in the process of crude oil refining. Bleaching is the process of removing impurities, colour pigments, traces of gums and soaps from vegetable oil. In the bleaching technology, bleaching earth is applied to crude oil, minimizing its content of pigments (e.g., carotenes and chlorophylls), heavy metals, and the phosphorus remaining after degumming. This improves the appearance and taste of the oil.
- Remove certain pigments such as carotinoids and chlorophyll
- Decompose and partially remove oxidation products
- Remove contaminants such as soaps and trace metals
- Remove traces of phosphatides
- Remove polycyclic aromatic hydrocarbons and other pollutants.
Bleaching process flow description
Bleaching is based on the principle of adsorption of unwanted substances onto bleaching earth. Reactions in the bleacher occur in conditions of deep vacuum and high temperature. The oil is pumped into the bleacher through the regenerative heat exchanger. Bleaching earth is dosed into the bleacher and mixed intensively for a determined time period.
After bleaching, the oil is pumped into a vertical pressure filter, where bleaching earth is retained and subsequently dried. The pressure leaf filter then releases bleached oil and bleaching earth falls out at specific intervals.
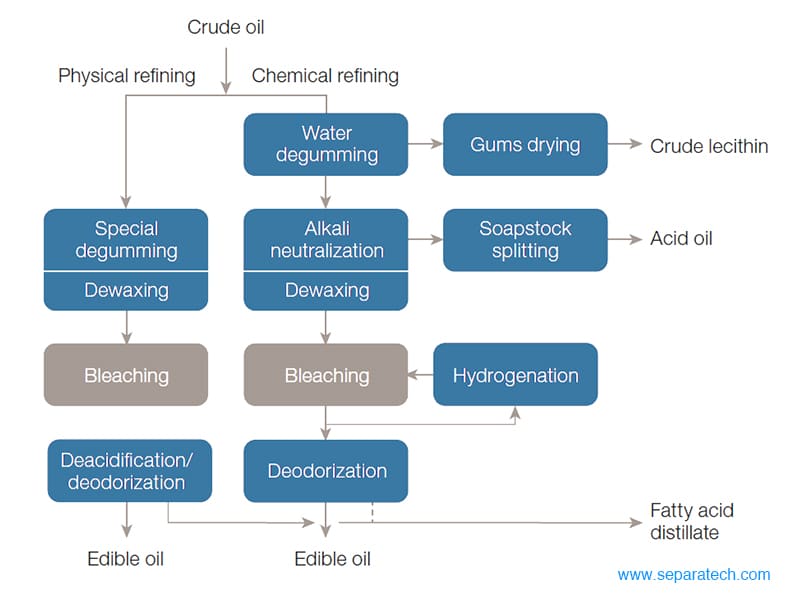
Pressure Leaf Filters
The pressure leaf filter is a closed filtration system and can be fully automated which results in less operator manipulation.
The regeneration time between the filtration cycles is short which reduces downtime.
The pressure leaf filter itself has no rotating parts, keeping maintenance to a minimum resulting in lower maintenance cost.
There are two main types of pressure leaf filters: vertical pressure leaf filters and horizontal pressure leaf filters.
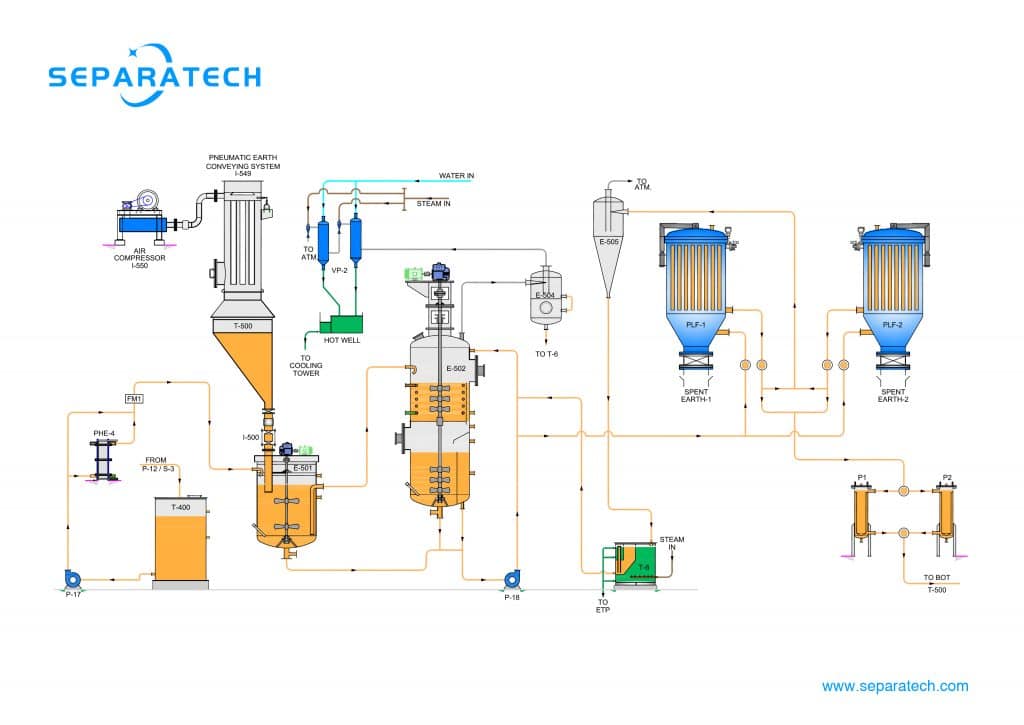
Supply scope
SEPARATECH supply vertical pressure leaf filters for bleaching / decolorization actions, ranging from 7 to 90 m^2.
Filtration leaf structure
The Leaves shall be of 5-layer design of the following construction.
4 X 4 mesh Centre Screen – 1
8 X 8 mesh Support Screen – 2
24 X 110 filter screen in Plain Dutch weave (PDW) – 2
Bleaching Mechanisms
During the bleaching process adsorption occurs via many different mechanisms involving various physical and chemical interactions; most of them improve the quality of the oil, but some of them may reduce it . These mechanisms include the following:
Adsorption ─ mechanism by which the sorbent binds a contaminant. This can occur in three different ways:
Physically through surface attraction involving van der Waals’ forces.
Chemically by “chemisorption” by electrochemical bonding to the surface of the clay.
By molecular sieves which trap contaminants under pressure inside the pores of the clay during filtration.
Absorption ─ mechanism by which the intra-granular pores are filled with some fluid—mainly oil — and in turn whatever contaminants came along with it. Oil retention is reported in two ways: as weight loss by Soxhlet extraction (with hexane being used as solvent), and as total organic matter determined by ashing.
Total oil retention depends on a number of variables including clay dosage levels, clay characteristics (e.g., particle size distribution and mineral type), permeability of the filter bed, incoming feedstock quality, cleanliness of the filter screen and the conditions used to purge the filter before disposal of the “spent” filter cake. Excessive oil retention increases the cost of running the process; oil loss through spent earth can typically range up to 35 weight percent solvent extractable and 50 weight percent for total organic matter of the earth used.
Filtration ─ mechanism of trapping or physically removing suspended contaminants: the physical act of filtering out the suspended clay that simultaneously removes the minor contaminants adsorbed to the clay particles. Filters used in the bleaching process include vertical pressure leaf filter, or horizontal pressure leaf filter ) and polishing filters (bag, cartridge, paper).
Catalysis ─ mechanism by which contaminants are degraded by interaction with the surface of the clay. For example, peroxides are effectively reduced (polymerized and/or decomposed into volatile oxidation by-products) by clay/oil interaction. With excessive heat and oxidation, pigments can form color compounds that are difficult to remove or said to be “fixed.” In the event of color fixation, red color is more difficult to remove by bleaching clays alone and resistant to thermal degradation leading to higher red color after deodorization.
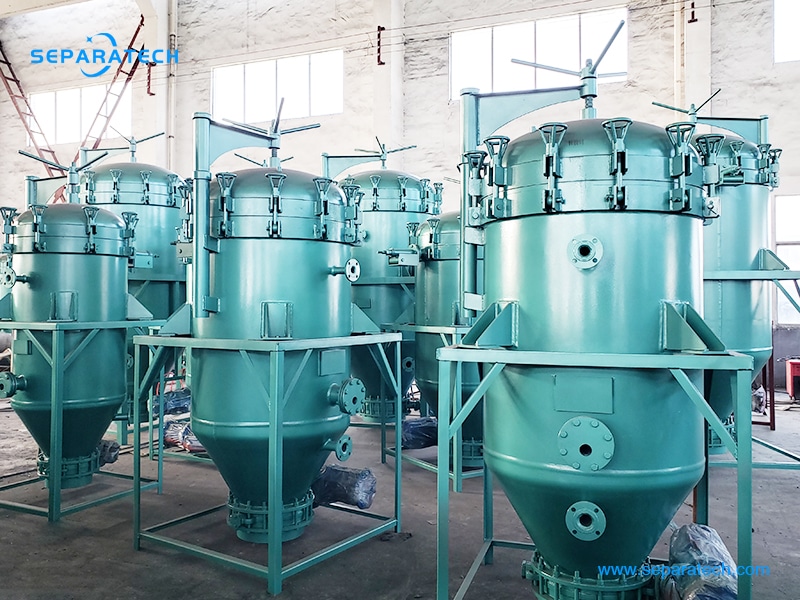
Typical pressure leaf filter for edible oil bleacing process:
• Avocado oil
• Palm oil
• Peanut oil / groundnut oil
• Rice bran oil
• Safflower oil
• Sesame oil
• Sunflower oil
• Olive oil
• Mustard oil